Total quality management (TQM) is that the method of detecting and reducing or eliminating errors in producing,and process of continuous improvement streamlining offer chain management, up the client expertise, and guaranteeing that workers
Total quality management aims to carry all parties concerned within the production method in charge of the quality of the ultimate product or service.
whereas there’s no wide agreed-upon approach, TQM efforts usually draw heavily on the previously developed tools and techniques of internal control.
TQM shares abundant in common with the Six sigma improvement method, it’s not constant as sigma.
TQM focuses on guaranteeing that internal pointers and method standards cut back errors, whereas Six sigma appearance to cut back defects.
key point
- Total quality management is process of identifying and reducing errors.
- focus on continuous Improvement
- Help to improve customer service, supply chain management and ensure employees are well trained.
- Improve the quality of organization
- TQM main aim is to improve production process accountability for the overall quality of product and services
Elements of total quality management
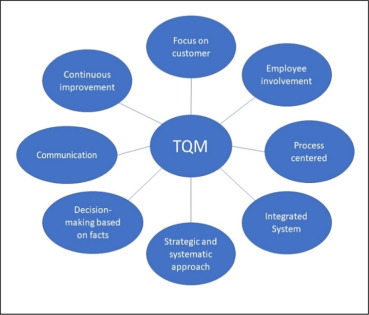
What is six sigma
six sigma is a method and technique of quality control establish in ninety-eighty six (1996) by Motorola, Inc. it was establish as a management a technique to avoid mistakes and work faster. Now it become organization standard with certifications offer to professionals.
Basically six sigma focus on statistical improvements of the business process. It involves qualitative measurements of success over qualitative markers. professionals of six sigma are those who business individuals who use financial analysis, project management and who use statistics to get improved functionality.